Welcome to “Ask Deb from QA,” an advice column from MxD.
Deb from QA — with decades of experience on the factory floor — will answer your questions to demystify and explain the digital manufacturing industry.
Please submit your questions to debfromqa@mxdusa.org
Q: Why are ‘microfactories’ showing up on so many manufacturing trends lists?
When this global pandemic disrupted the supply chain, we manufacturers had to become more nimble ASAP. That’s why there’s a buzz about microfactories. With all this uncertainty, companies want a way to be faster on their feet and closer to their customers and suppliers. Microfactories are one way to do that.
Just to be clear, we aren’t talking about Lilliputian versions of traditional mass-production factories. Microfactories can be small, sure. But they are less about size than about agility. These factories are light on capital expenditures, big on tech and automation, and usually go up fast. Tesla, back in 2018, needed another assembly line but had no time to build one. So in two weeks, it set up a microfactory in a tent in the parking lot of its Fremont, Calif., plant to crank out Model 3s.
Unlike Henry-Ford-esque factories that require lots of space, money, workers, and equipment, microfactories can open just about anywhere. They have a smaller carbon footprint. And being able to shift production lines on a dime means they can fill gaps or solve supply chain pinches.
For example, say you are an auto manufacturer in the United States and are buying a car part, like seats, from a company in China. You don’t want to risk running short of seats because of overseas COVID complications or some Pacific Ocean cargo jam. So you need a way to get those seats made closer to the plant where you put the cars together. One solution is opening a microfactory to make the seats. Then, once you’ve manufactured enough seats, you can shuffle things around to make glittery moon roofs or hot pink steering wheels. Like I said, a microfactory can react fast to changing needs and customer demands.
There’s a lot of neat microfactory stuff going on. Over in the United Kingdom, a startup called Arrival is building electric vans in a microfactory, using robots and human labor. They posted a fascinating video of what vehicle production looks like minus the assembly line.
Will 2023 be a macro moment for microfactories? Hard to say. Unlike the newly trendy “onshoring” and “reshoring” supply chain solutions, microfactories were around long before COVID-19 and the war in Ukraine brought the supply chain to its knees. The concept actually goes back to 1990 and the Mechanical Engineer Laboratory (MEL) of Japan.
But no less an authority than the World Economic Forum shared a column predicting that by 2029 “we’ll see cost-effective microfactories drive a new wave of innovation across industries as manufacturing becomes accessible to all people.”
Now that’s something to look forward to.
Want to keep up on what’s happening with the supply chain? Then sign up for ChainMail, the in-depth newsletter from MxD featuring the latest takes on modern supply chain trends and happenings.
Check out the last Ask Deb here:
Checking in with Chandra Brown
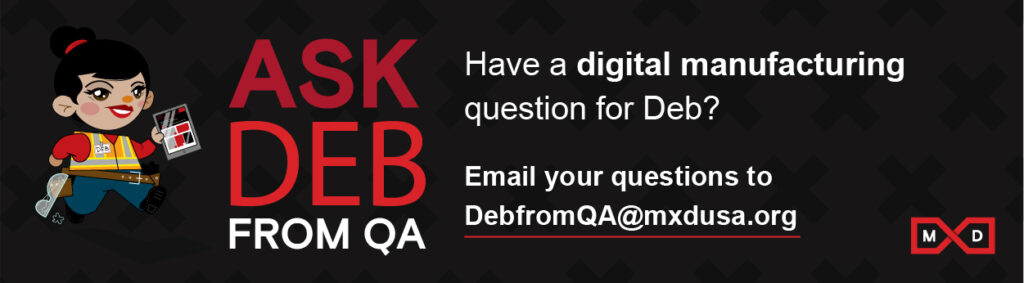
Deb from QA wants to hear your questions. Send ’em to debfromqa@mxdusa.org and she’ll answer as soon as the lights go back on.