Welcome to “Ask Deb from QA,” an advice column from MxD.
Deb from QA — with decades of experience on the factory floor — will answer your questions to demystify and explain the digital manufacturing industry.
Please submit your questions to debfromqa@mxdusa.org
Why am I hearing so much about lights-out factories lately? Haven’t they been around forever?
Good question! And while I wouldn’t say “forever,” lights-out factories go back to the days when Deb had big hair and a closet full of platform shoes — in other words, the early ’80s.
These 100% automated and mostly human-free factories rolled in as part of Industry 3.0, which you’ll recall emphasized automation. At a lights-out factory, there may be some quality assurance folks on hand, but no one is on the line and you can actually turn off the lights.
Adoption, though, has not exactly happened at lightning speed. After all, automation sounds great. But what happens when something falls off the conveyor line or a product doesn’t meet specification, and no human is there to figure out what to do?
That’s where Industry 4.0 comes in. My friends over at MxD tell me that new technology — like machine learning algorithms and data analytics — helps solve those kinds of challenges by adding cognitive skills to traditional automation.
Let’s say parts are on the conveyor and a robot’s grabbing them. Suddenly a part rolls toward the robot and tips over. A robot is still going to grab it and send it along. Yikes!
But if the factory has Industry 4.0 technology, it can deploy a vision system to take a picture of every part coming down the line and use machine learning to recognize patterns. If a part shows up that doesn’t fit the pattern, the technology has enough “intelligence” to register a, “Hey, wait a minute!” And it can tell the robot to turn the part right side up or remove it.
Industry bigwigs see a lot of benefits to this kind of manufacturing.
- One is consistency. While we humans are the best problem-solvers you are ever going to find, we aren’t perfect. We can’t do a million operations exactly the same way. But a robot can.
- Two, this is a great way to boost safety by getting robots to do hazardous tasks like painting or welding or dealing with chemicals, so humans don’t have to. And robots don’t even need a hazmat suit!
- Three, even companies flush with cash can’t find enough of us with the skills to fill all of the open jobs.
- Four, this can help address that skills gap. Instead of training a worker to put a bolt on a bumper, smart companies will train that worker to program a robot to do that task. Two problems solved!
This won’t work for everything. You aren’t going to see the Ferrari plant go lights-out anytime soon. But Fanuc has a lights-out factory in Japan where robots have been building other robots at a rate of 50 per shift since 2001. It can run unsupervised for 30 days at a time.
Now, I’m more Ferrari than Fanuc: Robots building robots is a bit futuristic for me. But, hey, I’m up for any bright idea — especially one that can keep me safer and out of a hazmat suit.
Check out the last Ask Deb here:
What’s a Human Digital Twin
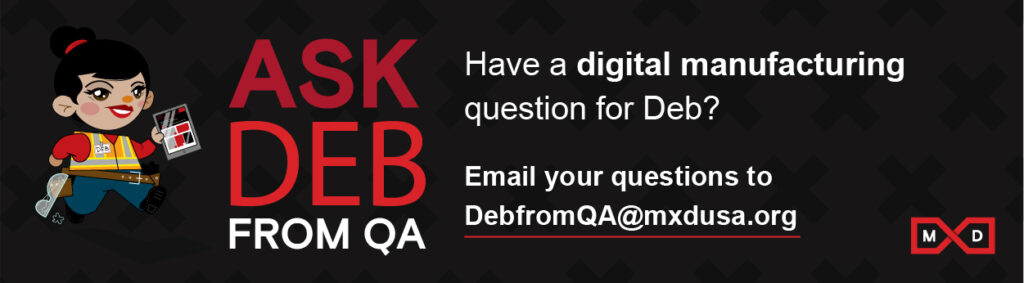
Deb from QA wants to hear your questions. Send ’em to debfromqa@mxdusa.org and she’ll answer as soon as the lights go back on.