On a sunny Southern California morning, the waters at the Port of Los Angeles are calm, but my mind is overwhelmed by the magnitude of operations.
From ships onto trucks or trains: I comprehend the idea of the supply chain in motion, transporting goods from factories in Asia to this southern stub of L.A., where thousands of containers are offloaded daily from vessels and then sent on their way via rail or tractor-trailer.
But put me on a boat cruising the channel, staring up at a massive cargo ship stacked high with containers being hoisted into the air by supersized gantries, and the scope just doesn’t quite compute. This mind-boggling view of the supply chain comes via a harbor tour arranged by the port, the busiest in the Western Hemisphere and a major choke point for goods during COVID chaos.
As we glide around the harbor, the vessel I’m gawking at, the NYK Vesta, is the length of nearly four football fields. It’s capable of transporting thousands of 40-foot-long steel containers laden with goods. A single one of those containers loaded onto a truck chassis is big enough to intimidate other drivers when hauled on a highway. So what’s it like to get up close to the Vesta with its containers stacked nine high and 16 across for the entire length of the ship? I scan the overwhelming pile and focus on several magenta-colored containers that stand out within a mountain of drab blue and green steel boxes. Each pinkish box looks like a Lego, or maybe a strawberry-flavored Kit Kat bar wafer. Perhaps inside is furniture, or auto parts, or apparel, three of the top imports to this port. Just multiply that one colorful 40-foot container by, oh about 5 million, and you’ve got the annual scope of the Port of L.A.’s activity.
Some port statistics help paint the picture. The industry measures cargo in TEUs, or twenty-foot equivalent units, meaning half the typical 40-foot container. Last year, amid COVID, the Port of L.A. did a record volume of 10.7 million TEUs. The Vesta, arriving from Japan after a two-week journey, has a container capacity of 9,012 TEUs. According to my back-of-the-envelope calculation, that’s the equivalent of about 3,600 50-foot tractor-trailers. Add it all up and the port brings ashore about 4 million big-rigs’ worth of stuff a year. Imagine that traffic jam. Speed and capacity are what matter here, and everything the port does has been stressed by COVID. During the January 2022 height of the backlog of vessels arriving to fulfill the demands of U.S. consumers, there were about 100 ships daily waiting offshore for a berth at either the Port of L.A. or next door’s Port of Long Beach. That backup is down to about 20 a day, which is still a headache compared to the before-times when there was no queue. Before COVID, 10 ships typically berthed at a time at L.A.; today, it’s 16. And yet despite more ships coming into the port, there are snafus.
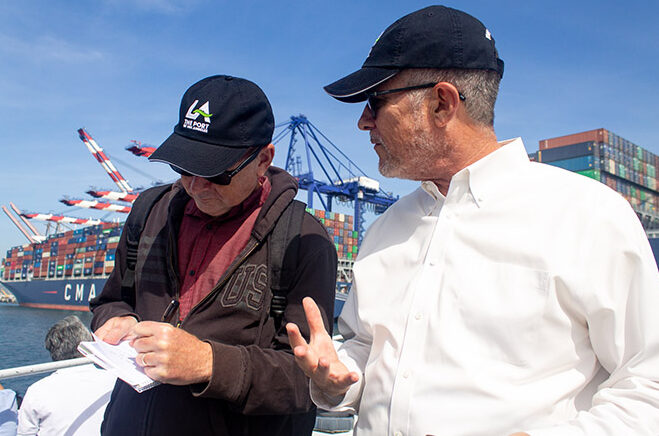
Michael Lev and Phillip Sanfield from the Port of L.A.
Photo credit Katia Butzen, MxD
The crisis of the moment is that containers once offloaded aren’t getting onto rail cars fast enough, so the steel boxes are piling up at the port. Cargo rail service in the U.S. is buckling under demand, hampered by shortages of rail workers and other problems. The average time containers at the Port of L.A. wait on the docks to be loaded onto rail is 7.5 days. Some wait nine days. Pre-COVID the average wait was two days, port spokesman Phillip Sanfield tells me as our boat cruises along.
One issue is cargo owners aren’t hurrying to grab their goods because warehouses are full. When I visited the port, there were 31,650 containers waiting for rail transport, 20,000 of which had been hanging around nine days or longer. Normally none would wait that long. Containers jamming the port have to be moved around more than once to make way for others, which slows operations. “You start losing efficiency if you get beyond a four-day dwell,” Sanfield says.
Ideally port operations are in sync. Ships arrive at night and are offloaded by dock workers on the 8 a.m. – 5 p.m. or 6 p.m. – 2 a.m. shift. Rarely, they also work a 3 a.m. “hoot” shift, but overtime is expensive. Normally it takes two to four days for the larger 12,000-15,000 TEU ships to be unloaded, be reloaded, and leave. COVID has added two to three days. Top exports include pet and animal feed, soybeans, wastepaper, fabric, and scrap metal. Given the U.S. trade deficit with Asia, it’s not surprising that many containers go back to Asia empty. They’re valuable because the shipping lines want them in Asia to be reused for the next round of imports. As they say at the port, “Our biggest export is air.”
Read Issue 16 of ChainMail here.
Enjoying this story? Subscribe to ChainMail, MxD’s newsletter on breaking supply chain news, trends, and updates.