April 28, 2022
Digital Twin Testbed for Process Manufacturing
This project will develop and implement a framework for collecting and aggregating various sensor data that will be necessary to build a digital twin of a product, process, and auxiliary equipment.
Manufacturers need to vet commercially available sensors, data aggregation solutions (enterprise and open architecture), AI data analytics packages, and cybersecurity solutions to understand utility and value for different processes and discrete applications. Yet, large manufacturers’ business environments often constrain their ability to experiment with the full array of sensor technologies, commercial offerings, and architectures. There is also a need for side-by-side comparison of discrete and process industry needs, especially through demonstrations in a manufacturing testbed environment.
Proposed Solution
The team will develop and implement a framework for gathering and analyzing all the data from a process manufacturing line necessary to improve visibility and control. They will also demonstrate a proof-of-concept ‘mobile worker’ solution onsite at MxD that can allow operators to receive tasks on a mobile device, access all data (such as environmental health and safety; process data; systems, applications, and products (SAP) related information; documentations; procedures; and alerts) to perform the task directly in the field, and update those inputs immediately to communicate the status to leadership.
Impact
The Digital Twin Testbed for Process Manufacturing at MxD will be open to MxD members and future projects for testing and experimenting with various digital twin or process manufacturing use cases, relating to predictive maintenance, cybersecurity, and other use cases. It will increase operational awareness and connected communications with operators and factory managers. Eventually, these technologies can be used to train or even perform activities on a digital twin of real-life process manufacturing activities. When these activities can take place virtually rather than in a physically challenging environment such as a chemical plant, workers can operate more safely and efficiently
Outcome
The process demonstration skid (PDS) built at the MxD Future Factory is accompanied by a full software stack designed to demonstrate the use of modern mobile technologies. This effort condensed a full stack of software designed to operate billion-dollar facilities into an accessible platform that helps develop understanding of the use and implementation of these new technologies.
From bottom up the system consists of the physical process, the process equipment, and the control devices, such as pressure, level, temperature, wireless temperature/vibration sensors; drive controls, control valve actuators; cables, switches, CPU, field units and architecture that feeds the servers and software on the plant bus level. There is an automation station, process historian and process device management maintenance station completing the traditional operational technology (OT) space.
On the information technology (IT) space there is a wide software stack serving design and optimization needs for the project, but also for improving the operations and maintenance relevant efficiencies. The software stack includes tools for 3D model authoring, 2D/1D authoring, validation and dynamic simulation of the process equipment, emulation of the control devices, manufacturing operations management, asset and process health monitoring, product lifecycle management, asset & operations dashboarding, operator and technician training, including for execution of installation, inspection, and maintenance tasks.
Read more about this Project
View a PDF of this Project's Powerpoint
From bottom up the system consists of the physical process, the process equipment, and the control devices, such as pressure, level, temperature, wireless temperature/vibration sensors; drive controls, control valve actuators; cables, switches, CPU, field units and architecture that feeds the servers and software on the plant bus level. There is an automation station, process historian and process device management maintenance station completing the traditional operational technology (OT) space.
On the information technology (IT) space there is a wide software stack serving design and optimization needs for the project, but also for improving the operations and maintenance relevant efficiencies. The software stack includes tools for 3D model authoring, 2D/1D authoring, validation and dynamic simulation of the process equipment, emulation of the control devices, manufacturing operations management, asset and process health monitoring, product lifecycle management, asset & operations dashboarding, operator and technician training, including for execution of installation, inspection, and maintenance tasks.
Read more about this Project
View a PDF of this Project's Powerpoint
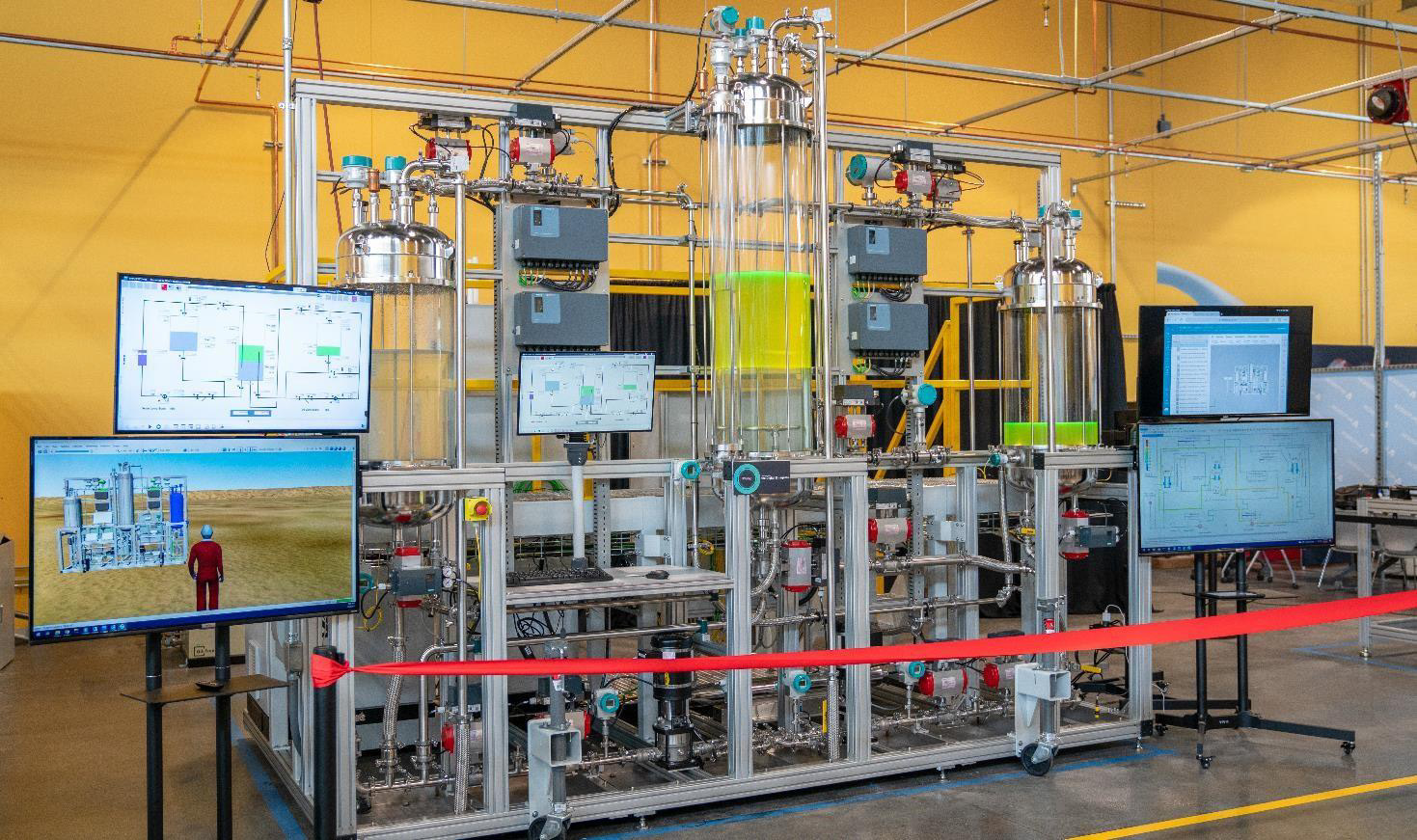
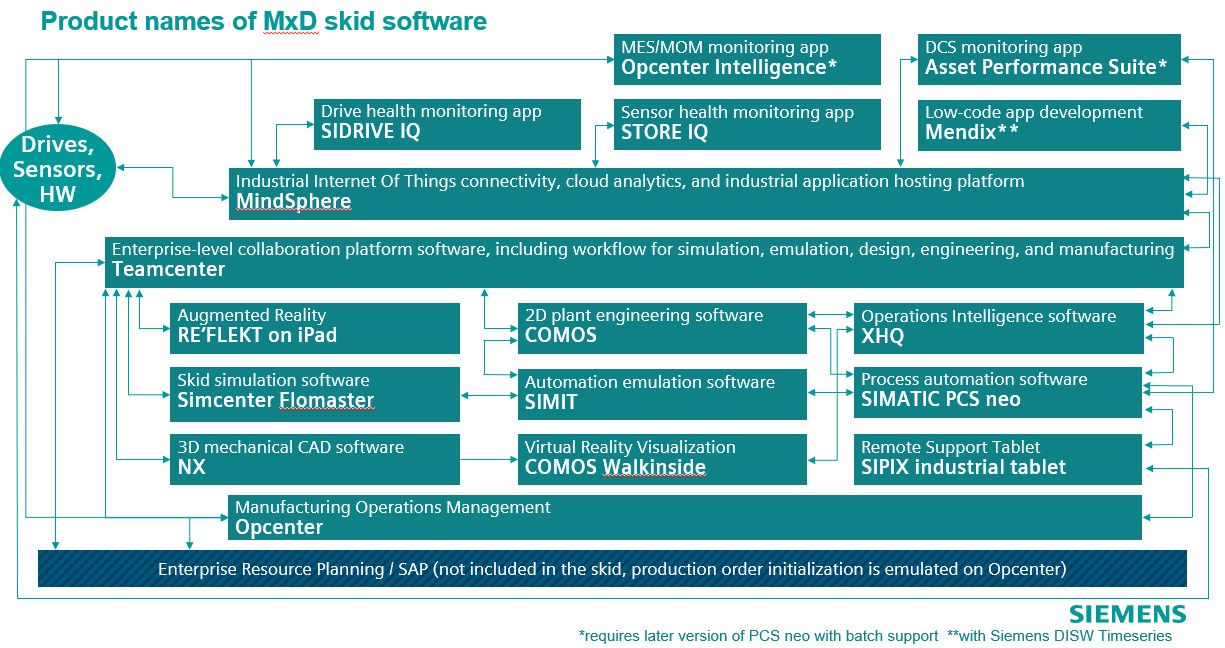