In the second of five parts of MxD and McKinsey & Company’s webinar series, executives from McKinsey and Fast Radius discuss what makes a “lighthouse manufacturer” and how end-to-end digitization can prepare companies to weather the next global crisis.
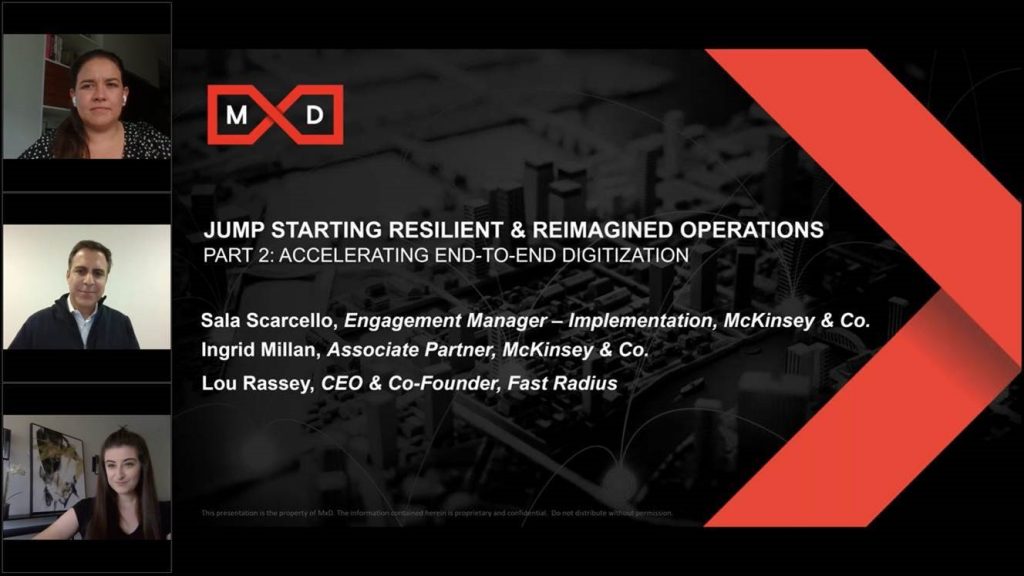
Ingrid Millán, Associate Partner at McKinsey and one of the leaders in its North American Digital Supply Chain practice, explained that lighthouse manufacturers are at the forefront of the fourth industrial revolution and have overcome “pilot purgatory,” making significant impact at scale.
In 2018, McKinsey and the World Economic Forum gave 16 leading factories this designation. The following year, 28 new sites joined the community, including 14 sites that have connected their value chains end-to-end. Fast Radius was the first lighthouse manufacturer identified in the United States.
All have pushed boundaries in digital strategy and automation, achieving impact not just in one use case but in 15 to 20 use cases along their value chains.
Ingrid outlined six value drivers: technology democratization and augmenting the operator, big data decision-making, process and business model innovation, customer centricity, seamless connectivity across functions, and continuous connectivity across organizations. The latter three drivers are specific to lighthouse manufacturers that have accomplished end-to-end digitization.
The far-reaching challenges of the COVID-19 pandemic have provided a testing ground for lighthouse manufacturers to flex their digital manufacturing muscle.
Industrial demand has slowed across most segments, with a massive demand surge for certain critical goods. Traditional time to design and launch does not meet the need for the most in-demand products. Major supply disruptions are occurring as global trade slows or halts, leading many companies to look for new suppliers. There are novel risks to people as they experience new working routines for both factories and offices.
Amid all these changes, governments are leaning on World War II-era approaches to try to help, and distrust and anti-globalization dialogue fuels uncertainty.
How can manufacturers contend with this difficult environment? Lou Rassey, Co-Founder and CEO of Fast Radius, a leading provider of additive and on-demand manufacturing solutions, described the four responses his team and partners have employed.
1) Discover: Sharing Design and Manufacturing Insight
Platforms for digital collaboration exist now that were not around five years ago, making it easier to assemble the right technologies, tools, and partners to engage in solving a problem.
In one example, Fast Radius brought together a relevant group of designers and manufacturers to share designs for face masks on a platform that allowed participants to build upon previous designs. In just a few days, the community was able to create a viable, manufacturable design, that could support the local need. Sharing and iterating on these lessons in the discovery stage would not have been possible without the most current technology.
2) Design: Engineer New, Complex Products Embracing Full Suite of Industry 4.0 Tools
New tools of digital design and manufacturing are making it possible to significantly cut down new product development time and engineer previously impossible geometries.
In early days of the COVID-19 crisis in the United States, Fast Radius collaborated with Carbon and Resolution Medical to address a diagnostic swab shortage. The shortage of this instrument, a Class I Medical Device, was identified in mid-March, and by early April a first-generation swab was available. This involved 30 design iterations in just 18 days.
Early tests suggest the additively manufactured swabs perform at least as well as traditional ones and may lead to fewer false negatives because of the attributes of the updated design and material.
3) Make: Flexible Digital Manufacturing to Allow Repurposing of Assets
Digital production enables a more flexible response when there are large swings in demand and supply as during a pandemic. Connecting a robust digital thread from design through production and qualification can allow rapid, high-quality scale-up.
Fast Radius was able to shift additive manufacturing production to making personal protective equipment, diagnostic equipment, and swabs, including making more than 106 thousand face shields as of August 2020. Digital manufacturing technology enabled fast pivots – instead of taking weeks to ramp up production in a new area, it took days.
In addition to the technology side, Fast Radius had invested in its people, building strength, agility, and innovation in a way that prepared the company for a critical juncture. New skills, working models, and organization structures, are also important investments that companies should consider that are relevant for all levels and roles.
4) Fulfill: Digital Manufacturing and Logistics Can Unlock New Hyper-Scaling and On-Demand Fulfillment
Fast Radius has established a virtual warehouse rather than a physical one with some clients, meaning items are produced on demand and in the specific quantity needed.
With COVID-19 overwhelming hospitals in some regions early in the pandemic, a shortfall of millions of ventilators was anticipated. Best efforts from many companies to traditionally manufacture and scale would produce thousands of devices in a month, versus hundreds of thousands feared to be necessary. Large-scale manufacturing and supply chain problems need scalable solutions.
As it turned out, the number of ventilators needed was not as high as some initial predictions. But in the next crisis, whether they are ventilators, other medical equipment, or a different product entirely, digital manufacturing and logistics will be necessary to achieve hyper-scale manufacturing to meet the urgent need.
Ultimately, Industry 4.0 is ushering in a new era of manufacturing to make new things possible. Lighthouse manufacturers, as suggested by their moniker, are illuminating the way for the sector.
If you missed this webinar, you can access the recording in MxD’s webinar library. Tune into the remaining parts of the five-part series by registering on MxD’s website. And read the McKinsey article that inspired the webinar collaboration here.
Special thanks also to Sala Scarcello, Engagement Manager – Implementation at McKinsey, for moderating the discussion.