Welcome to “Ask Deb from QA,” an advice column from MxD.
Deb from QA — with decades of experience on the factory floor — will answer your questions to demystify and explain the digital manufacturing industry.
Please submit your questions to debfromqa@mxdusa.org
Q: What is ‘predictive maintenance’ and why do I keep hearing so much about it?
Nothing says “bad day” quite like a machine breaking down. And predictive maintenance is one way to help minimize surprise — and expensive — factory floor downtime due to equipment failure.
You’re hearing so much about predictive maintenance because more companies are implementing it now that they have the Industry 4.0 digital tools that make it possible.
But I’m getting ahead of myself. Let’s do a quick refresher.
When we talk about maintenance, there’s “reactive” — or not doing anything until something breaks — or “proactive,” which means acting before you’ve got a problem.
Predictive maintenance is under the proactive umbrella, along with preventive maintenance and condition-based maintenance.
Preventive maintenance is done on a schedule, like getting your car’s oil changed every 5,000 miles whether that 10W-40 is nasty or not.
Condition-based maintenance takes things up a notch, relying on sensors and software to figure out exactly when action is required. For instance, if I need to keep a tank of water at a certain level, I fill it only when the sensors alert me that the water level is down — and not on a seemingly arbitrary schedule.
And then we have predictive maintenance. Like with condition-based maintenance, you’re still monitoring, but now you’re analyzing data that’s been captured via the industrial internet of things (IIoT). Machine learning and algorithms are helping you decipher historic trends so you can actually schedule maintenance when it’s truly needed and predict when a machine, or a component, is going to hit the skids.
Predictive maintenance can put you ahead of the competition by saving money and limiting downtime, And in a world where there are never enough people to get all the work done, ensuring that employees are doing what’s most needed instead of frantically dialing 1-800-REPAIR or running to fill the water tank when the sensor sends out an alert.
If you need an example, McKinsey & Company, which partners with my friends at MxD, recently shared some Industry 4.0 transformation insights, including how a European auto company’s use of predictive maintenance reduced unplanned downtime on one of their crucial assets by 25 percent.
Now, aging equipment can seem like a hurdle to getting in on this digital action. After all, you aren’t going to toss a perfectly fine machine just so you can collect some data. Fortunately, there are retrofitting options, with companies standing by to partner with you on ways to add sensors and more to older assets.
MxD has a nifty Sensor Retrofit Project show-and-tell as part of its Virtual Factory Floor Tour. With a manual knee-and-column mill as the star of the show, they demonstrate what retrofitting can look like.
In this case, a current sensor has been installed on the power line that goes to the mill’s spindle motor. That sensor indicates when the motor is on and such things as how much current it’s drawing. In other words, data is being captured from a legacy piece of equipment, with that data helping to predict when the motor will need maintenance, like a bearing repair, or how many hours are left before it goes kaput.
So folks, you can leave the tarot cards at home. There’s a new way to see the future, and it’s a lot more accurate.
Check out the last Ask Deb here:
Understanding the Low-Code Buzz
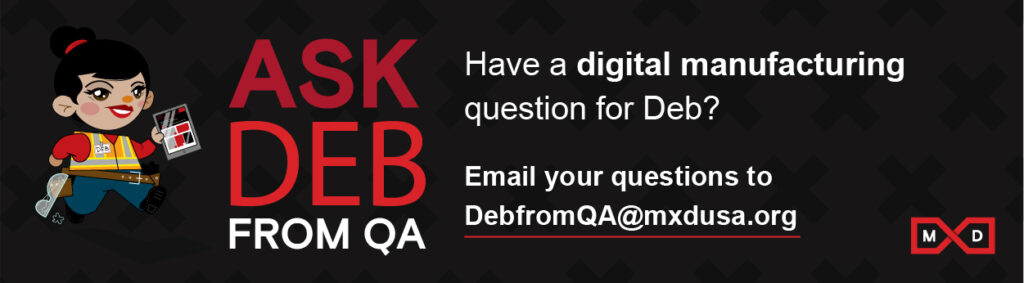
Deb from QA wants to hear your questions. Send ’em to debfromqa@mxdusa.org and she’ll answer as soon as the lights go back on.