Welcome to “Ask Deb from QA,” an advice column from MxD.
Deb from QA — with decades of experience on the factory floor — will answer your questions to demystify and explain the digital manufacturing industry.
Please submit your questions to debfromqa@mxdusa.org
Q: What’s the difference between “digital engineering” and “systems engineering?” I guess digital engineering is the new stuff I have to learn. And I see that each of them has its own “body of knowledge.”
— Dan Rusin, government engineer, U.S. Army Aberdeen Proving Ground, Maryland
Thank you for your great question, Dan! And you are spot on. Digital engineering is indeed the “new stuff.” It’s considered key to manufacturing’s digital transformation journey and is getting a lot of attention.
One way to think of it is that systems engineering is more traditional, while digital engineering uses innovative technology and all that new data we’re collecting in the factory to take things up a notch. Both play essential roles in manufacturing, however, and are complementary. And in smaller factories, the same person may be doing both jobs.
According to my friends over at MxD, digital engineering is all about gathering, capturing, integrating, analyzing, and using data to increase efficiency and reduce errors throughout the manufacturing process.
Systems engineers also help factories be as efficient as possible, but they are looking at the overall picture, everything from the assembly line to being on time and developing, maintaining, and improving systems.
To get at the nitty-gritty of the differences, I turned to Rodrigo Perez, systems integration engineer for MxD.
“Systems engineering is much broader than digital engineering,” Rodrigo told me.
Systems engineers coordinate a lot of moving parts and subsystems to ensure that quality requirements are met, that industry standards and best practices are maintained, and that nothing goes wrong during the manufacturing process, he added.
Digital engineers, meanwhile, are relying on data and digital technologies to design, simulate, and optimize systems. For example, Rodrigo explained, computer-aided design (CAD) software and other simulation tools let these engineers create virtual representations of instances, allowing them to kick the tires without ever starting any machines. That means reduced costs for things like tooling and less risk of do-overs.
The virtual representations include digital twins that are digital replicas of things IRL, as the kids say, or in real life. Manufacturing is just one industry that’s had big success with digital twins. Rolls-Royce, for instance, is using digital twins to pump up its physical manufacturing, according to CNBC, which just did a report on factories of the future. Rolls-Royce engineers, according to that story, “create precise virtual copies of its jet engines and then install sensors and satellite networks on-board to feed back data to the digital copy in real time.”
Other manufacturers are taking data from sensors on factory floor equipment and using artificial intelligence tools to analyze it. That enables the predictive maintenance that helps keep machines humming. With all these digital bells and whistles, we get so much more insight into what our manufacturing systems are doing and can minimize cursed down time.
The way I see this is that systems engineers are like orchestra conductors, making sure all the musicians are hitting the right notes at the right time. Digital engineers are like the composers tapping out new music on their laptops. They can test out new tunes without anyone booing and even cue violins without having to pester any real violinists. Both make beautiful music but approach it in different ways.
As you note, Dan, each of these disciplines has its own body of knowledge: Digital Engineering Body of Knowledge (DEBoK), compiled by the Department of Defense, and Systems Engineering Body of Knowledge (SEBoK). These are detailed descriptions of what these engineering fields involve, and having two of them may complicate things. But it makes sense because despite their overlap, each has distinct areas of expertise.
I hope all this information helps, Dan, and good luck with your learning!
Curious about the latest manufacturing trends? MxD’s 22,000-square-foot research factory tests and demonstrates a range of new technologies.
Check out the last Ask Deb here:
Why the Buzz About Microfactories?
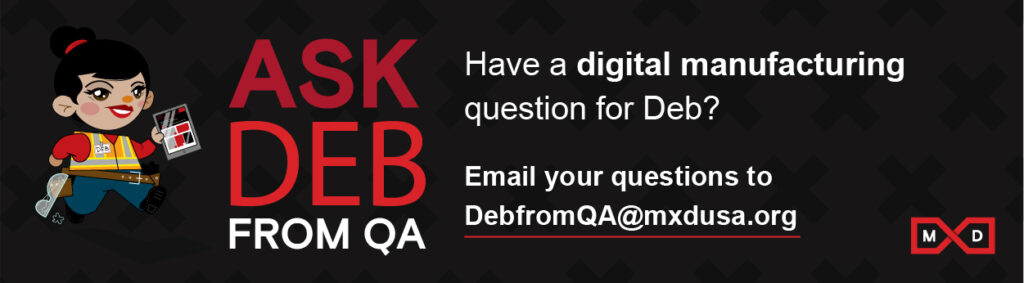
Deb from QA wants to hear your questions. Send ’em to debfromqa@mxdusa.org and she’ll answer as soon as the lights go back on.